
materials in ball mills
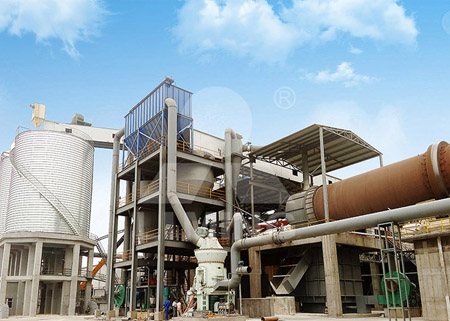
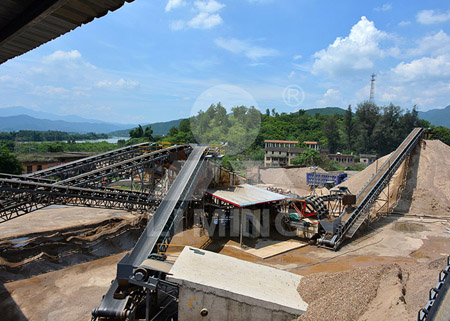
materials in ball mills
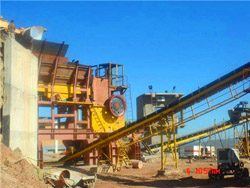
(PDF) Grinding Media in Ball Mills-A Review
One of the most used tumbling mills is the ball mill. This paper reviews different types of grinding media that have been developed and improved over the years and their properties.The ball mill Ball milling is a mechanical technique widely used to grind powders into ne particles and blend materials.18 Being an environmentally-friendly, cost-effective Ball milling: a green technology for the preparation and
احصل على السعر
(PDF) Grinding in Ball Mills: Modeling and Process
A ball mill is a type of grinder widely utilized in the process of mechanochemical catalytic degradation. It consists of one or more rotating cylinders partially filled with grinding...For most applications in organic synthesis, including catalysis, ceramic materials (e.g. ZrO 2) are the best choice. They are chemically inert and the material Ball Milling in Organic Synthesis: Solutions and Challanges
احصل على السعر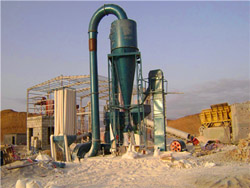
Ball Mill an overview ScienceDirect Topics
The balls are initially 5–10 cm diameter but gradually wear away as grinding of the ore proceeds. The feed to ball mills (dry basis) is typically 75 vol.-% ore and 25% steel. The In this paper, we report on a detailed experimental analysis of the long-term grinding behavior of silica sand as a model material in an oscillatory ball mill for a Evolution of grinding energy and particle size during dry ball
احصل على السعر
Ball Mill an overview ScienceDirect Topics
where d b.max is the maximum size of feed (mm); σ is compression strength (MPa); E is modulus of elasticity (MPa); ρb is density of material of balls (kg/m 3); D is inner diameter of the mill body (m).. Generally, a maximum allowed ball size is situated in the range from D /18 to D/24.. The degree of filling the mill with balls also influences productivity of the mill The ball mill Ball milling is a mechanical technique widely used to grind powders into fine particles and blend materials. 18 Being an environmentally-friendly, cost-effective technique, it has found wide Ball milling: a green technology for the
احصل على السعر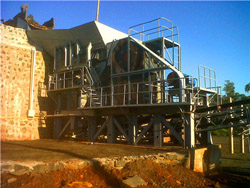
The effects of grinding media shapes on the grinding kinetics
The effects of material ball ratio, medium size and proportioning, stirring speed, grinding concentration, and medium filling rate [29–32] on the stirred mill grinding were investigated. Under the appropriate grinding conditions of the ceramic-medium stirred mill, extended-continuous grinding and magnetic separation experiments were conductedPlanetary Ball Mills (Figure 5 a) are commonly utilized mills in MA and MD processes for synthesizing nearly all types of metastable, At the turn of the century, several ball mill manufacturers started to produce cryo-ball mills, which grind the desired materials under a flow of liquid nitrogen. It is designed specifically for cryogenicMechanical Milling: A Superior Nanotechnological Tool for Fabrication
احصل على السعر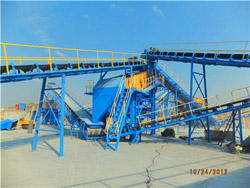
Materials Development Using High-Energy Ball Milling: A
High-energy ball milling (HEBM) of powders is a complex process involving mixing, morphology changes, generation and evolution of defects of the crystalline lattice, and formation of new phases. This review is dedicated to the memory of our colleague, Prof. Michail A. Korchagin (1946–2021), and aims to highlight his works on the synthesis of In this paper, we report on a detailed experimental analysis of the long-term grinding behavior of silica sand as a model material in an oscillatory ball mill for a broad range of the values of vibration frequency and amount of powder. We show that the re-agglomeration of fine particles unambiguously explains the anomalous increase of Evolution of grinding energy and particle size during dry ball
احصل على السعر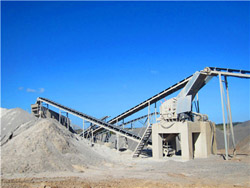
Flow of materials in rod mills as compared to ball mills in dry
In the case of ball mills, the axial dispersion is higher and the mean residence time is shorter than those in rod mills. In rod mills, the axial dispersion is lower—close to plug flow ( Lynch, 1977 )—as well as selective breakage (compared with ball mills) produce a narrower size distribution product than that of ball mills.Abstract and Figures. This work focuses on the characterization of heat generation during dry fracture by direct impact of a tantalum ore. Moreover, an attempt was made to quantify the heat energyHeat generation model in the ball-milling process of a tantalum
احصل على السعر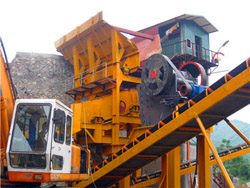
Impact energy of particles in ball mills based on DEM
Ball mill is one of the most commonly used mills for the crushing and grinding of mineral ore. It is generally used to grind material down to the particle size of 20 to 75 μm and can vary in size from a small batch mill up to a mill with outputs of hundreds of tonnes per hour.For grinding as well as mechanochemical reactions the stressing conditions within the different ball mills are decisive. As generally accepted and defined by Kwade and co-workers [] in detail, the stressing conditions in mills are defined by following mechanisms.. Stressing type: Arrangement of particles during stressing (single particles, layer of particles, bed of Energy Storage Materials for Solid‐State Batteries: Design by
احصل على السعر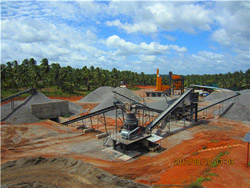
Ball Milling in Organic Synthesis: Solutions and Challanges
(planetary ball mill, mixer ball mill, vibration ball mill, ). • The scale of reaction determines the size and the type of ball mill. • Vessels for laboratory vibration ball mills are normally restricted to a volume of 50 cm3. Milling material: • The material density determines the energy entry and therefore, the choice of materialImportant advances have been made in the last 60 years or so in the modeling of ball mills using mathematical formulas and models. One approach that has gained popularity is the population balance Optimization of Solids Concentration in Iron Ore
احصل على السعر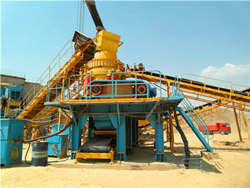
Full article: Mechanical alloying: a critical review
Mechanical alloying (MA) is a powder process that consists of repeated cold welding, fracturing, and rewelding of powder particles in a high-energy ball mill. This process is capable of synthesizing different types of non-equilibrium phases including supersaturated solid solutions, nanocrystalline materials, metallic glasses, high-entropyProcesses inside planetary ball mills are complex and strongly depend on the processed material and synthesis and, thus, the optimum milling conditions have to be assessed for each individual system.Chem Soc Rev ResearchGate
احصل على السعر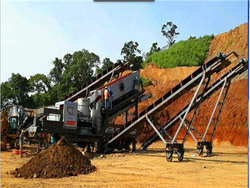
Ball milling: a green technology for the preparation and
The ball mill Ball milling is a mechanical technique widely used to grind powders into ne particles and blend materials.18 Being an environmentally-friendly, cost-effective technique, it has found wide application in industry all over the world. Since this mini-review mainly focuses on the conditions applied for the prep-a) Schematic representation of a ball mill (horizontal section); (b) different types of instruments (this figure has been adapted from ref. 19 with permission from Royal Society of Chemistry).(PDF) Ball milling : A green technology for the preparation
احصل على السعر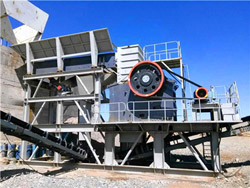
Model Study of Mechanicochemical Degradation in a Planetary Ball Mill
The process of ball milling and the materials that compose planetary ball mills are highly complex, and the existing research on the change in ball-milling energy is not mature. The theoretical model of a ball mill was established for the first time to simulate the motion, collision process, energy transfer, and temperature change of small balls during Sl is the specific rate of breakage of size 1 material, fraction per unit time. If Sl is con stant with time, as the contents of the mill grind finer, eqn. (1) integrates to log w, (t) -log w, (0) = -S, t/2.303 (2) This is referred to as the first-order hypothesis of grinding. Plotting experimental values of wl (t) versus t on log-linear scalesBreakage properties of some materials in a laboratory ball mill
احصل على السعر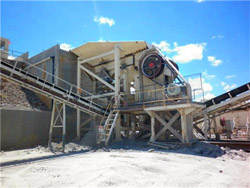
Ball milling as an important pretreatment technique in
The forces acting on the lignocellulosic material in planetary ball mills are much higher than the forces acting on the material in other mill types. A comparative study of the effectiveness of using tumbling, attrition, and planetary ball milling for pretreatment of rice straw suggested that planetary ball milling was the most effective toBall mills find applications across many disciplines, from materials research to chemical analysis and even biological research [78,79,80]. Ball milling is a process that utilizes mechanical forces, such as those generated by the rotating jar of a ball mill, to break up the material into smaller pieces and mix them together .Producing Metal Powder from Machining Chips Using Ball
احصل على السعر