
power consumption of ball mill
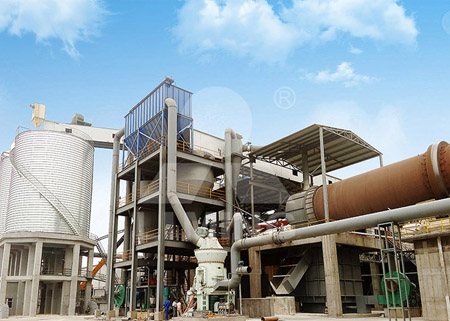
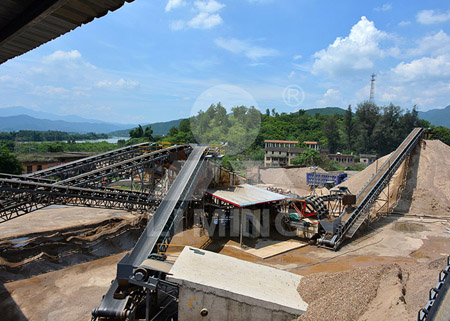
power consumption of ball mill
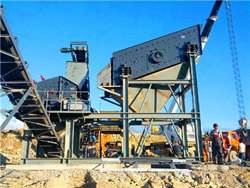
Charge behaviour and power consumption in ball mills:
The change in power consumption between the best and worst lifter shapes is now 8.4%. ⋅ For a mill speed of 100%, the lowest specific power occurs for new lifters. Energy consumption increases as the lifters wear and is still increasing even at 22.5°, by Typical power consumption for a 5-m diameter by 7-m-long ball mill is between 2.5 and 3.5 MW. The actual proportion of this energy usefully used in size Charge behaviour and power consumption in ball mills:
احصل على السعر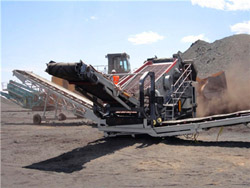
Charge behaviour and power consumption in ball mills:
Many authors have used DEM to investigate the effect of the lifter profile on the charging behavior and power draw within industrial mills (Powell, 1991; Cleary, Owing to the lack of effective energy consumption models of ball mills in the ceramic industry, a calculation model to forecast energy consumption of ceramic ball mills during Calculation method and its application for energy consumption of ball
احصل على السعر
Ball charge loading impact on specific power consumption
Ball charge loading impact on specific power consumption and capacity. Abstract: In determining the proper mill size required to meet a targeted production rate, When the mills charge comprising 60% of small balls and 40% of big balls, mill speed has the greatest influence on power consumption. When the mill charge is Effects of Ball Size Distribution and Mill Speed and Their Interactions
احصل على السعر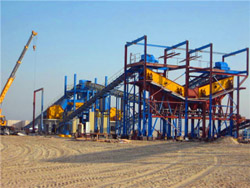
Energy conservation and consumption reduction in
Compared with the original two-stage ball milling process, the cost of grinding power consumption is significantly reduced by about 50.16%, which provides a The specific comminution energy for milling in the Bond test mill appears to be based on 60 J/rev, which defines the net energy required in the Bond ball mill to realise the same grinding...(PDF) Measurement of electrical energy
احصل على السعر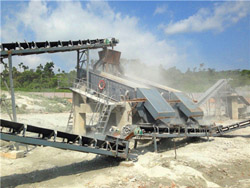
Charge behaviour and power consumption in ball mills:
Charge behaviour and power consumption in ball mills: sensitivity to mill operating conditions, liner geometry and charge composition Semantic Scholar. DOI: mm were replaced with 80 mm balls to reduce the amount of coarser particles in circulation. Larger balls reduced the number of particles coarser than 1 mm by about 5%. In case the feed to ball mill was equal to 1200 Mg/h, it resulted in a reduction of 60 Mg/h of the weight of coarse particles in circulation. It also enabled the processing of aAnaliza efektywności mielenia w młynach kulowym i
احصل على السعر
Charge behaviour and power consumption in ball mills:
The size of grinding media is the primary factor that affects the overall milling efficiency of a ball mill (e.g. power consumption and particle size breakage). This article tackles the lack of aBall mill and other machines. The energy consumption of a ball mill can be calculated as follows: Measure the operating time of the mill. Measure the power input to the mill using a power meterHow to calculate the energy consumption of a ball mill?
احصل على السعر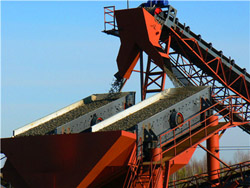
Ball Mill an overview ScienceDirect Topics
They have lower specific energy consumption than ball mills and the separator, as in raw mills, is integral with the mill body. In the Loesche mill, Fig. 2.23, 16 two pairs of rollers are used. In each pair the first, smaller diameter, roller stabilises the bed prior to grinding which takes place under the larger roller. Manufacturers usemode of energy consumption in the mill. Bian [7] investigated the effect of lifters and mill speed on particle behaviour, the changes in the torque and power consumption of a ball mill can be effectively explained using two important factors: lifter and particle area ratio. Generally, optimization of powerPAPER OPEN ACCESS Effect of Lifter Shapes on the Mill
احصل على السعر
Ball Mills 911 Metallurgist
In order to get the most economical consumption of power, the ball load in a Hardinge Mill should be kept up to the level of the trunnions. The capacities, power requirements, etc., of the various sizes of Hardinge Ball Mills are given in Table 12. It should be noted that the two figures describing the size of a mill represent the diameter ofBall mill optimisation As grinding accounts for a sizeable share in a cement plant’s power consumption, optimisation of grinding equipment such as ball mills can provide significant cost and CO 2 emission benefits to the cement producer. n by Thomas Holzinger, Holzinger Consulting, Switzerland BALL MILLS 1 FEBRUARY 2021 INTERNATIONAL BALL MILLS Ball mill optimisation holzinger
احصل على السعر
Charge behaviour and power consumption in ball mills:
Discrete element method (DEM) modelling has been used to systematically study the effects of changes in mill operating parameters and particle properties on the charge shape and power draw of a 5-m ball mill. Specifically, changes in charge fill level, lifter shape (either by design or wear) and lifter pattern are analysed. The effects of (Y-La-Ce-Nd-Gd) 2 O 3+β high-entropy rare earth oxides (HE-REOs) were synthesized using both mechanochemical (ball milling) and chemical (sol-gel) methods. Energy-dispersive X-ray spectroscopy revealed that the compositional uniformity of the as-synthesized powders was the highest in the sol-gel process, followed by that in wet A comparative study on a newly designed ball mill and the
احصل على السعر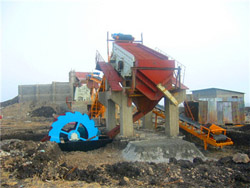
Effect of lifters and mill speed on particle behaviour, torque,
The changes in the torque and power consumption of ball mills can be effectively explained using two important parameters: lifters and particle area ratio. The torque of liners and baffles is also examined when the operating parameters of ball mills are changed. The results indicate that lifter height, lifter number, and mill speed affect theOur paper presents the hammer mill working process optimization problem destined for milling energetic biomass (MiscanthusGiganteus and Salix Viminalis). For the study, functional and Sustainability Free Full-Text Optimization Issues
احصل على السعر
(PDF) Energy conservation and consumption reduction in
Grinding ef ciency is the unit energy consumption rate of the mill, which represents the amount of material with a particle size of − 0.043 mm newly generated for every 1 kW • h of energyThe main equipment for grinding construction materials are ball-tube mills, which are actively used in industry and are constantly being improved. The main issue of improvement is to reduce the power consumption of a ball-tube mill with cross-longitudinal movement of the load. A comparative analysis and the possibility of using the knownPower Calculation of Ball-Tube Mill Drives in the
احصل على السعر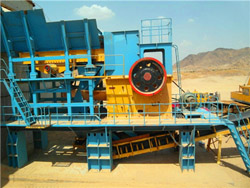
Determination of power consumption for suspension
The power consumption of the stirred ball mill was determined by a method based on the dimensional analysis. In this case the stirring equipments have similar geometry. The specific mathematicalThe aim of these calculations is simply to determine the total energy limit of the milling bodies for each mill. 2.6.2. Milling energy consumption. For all experiments, the power of the milling devices was measured using a PX 120 wattmeter (METRIX, France) connected to WattCom (USA) data acquisition software, and the mean power over the Comparative comminution efficiencies of rotary, stirred and
احصل على السعر
A Comparative Study of Energy Efficiency in Tumbling Mills
Tumbling mills are notorious for their low energy efficiency because they only use up to 10% of installed power for grinding action. A feature of ball mills is their high specific energy consumption; a mill filled with balls, working idle, consumes approximately as much energy as at full-scale capacity, i.e., during the grinding of material.A significant power saving of 39.2% was observed for the dry VRM compared to the wet ball mill (37.7% for the circuit). while the reduced power consumption combined with the decrease in grinding media and wear component consumption resulted in a 5.9% reduction in the operating expenditure (OPEX). The viability of the VRM in this A Technical and Economic Comparison of Ball Mill Limestone
احصل على السعر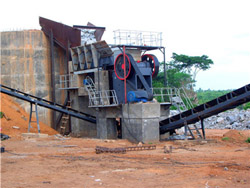
The Effect of Grinding Media on Mineral Breakage Properties
The breakage and liberation of minerals are the key to fluidized mining for minerals. In the ball milling process, steel balls function as not only a grinding action implementer but also energy carrier to determine the breakage behavior of ores and the production capacity of the mill. When ground products present a much coarse or much Tumbling mills are notorious for their low energy efficiency because they only use up to 10% of installed power for grinding action. A feature of ball mills is their high specific energy consumption; a mill filled with balls, working idle, consumes approximately as much energy as at full-scale capacity, i.e., during the grinding of material.A Comparative Study of Energy Efficiency in Tumbling Mills with
احصل على السعر