
concentration of ore hematite process
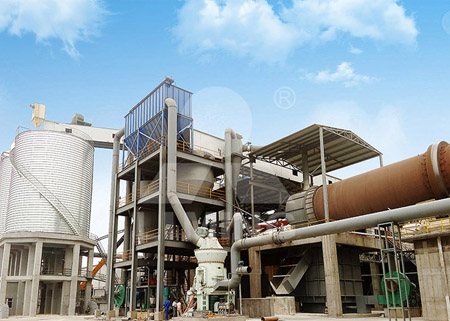
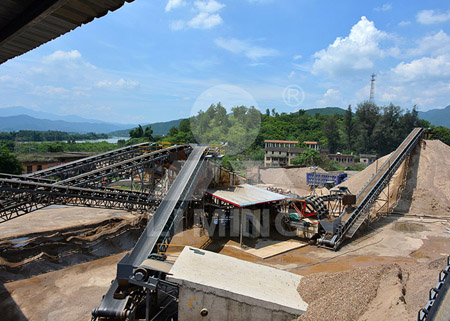
concentration of ore hematite process
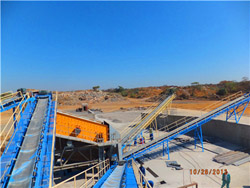
Mineral and Technological Features of
The BHQ ore was assayed as 38.9wt% Fe, 42.5wt% SiO2, and 1.0wt% Al2O3. In this ore, hematite and quartz are present as the The selective flocculation dispersion process for hematite ore concentration begins with crushing and grinding the hematite ore to the liberation size of Water chemistry analysis of an industrial selective
احصل على السعر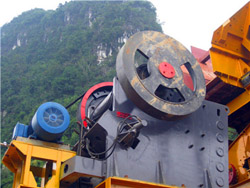
Kinetic characterization of flash reduction process of hematite ore
, Chunsong Wang a c,Lei Shao a c,Zongshu Zou b c Add to Mendeley https://doi/10.1016/j.ijhydene.2020.08.196 Get rights and content Highlights • CFD Therefore, there is an urgent need to develop a low-cost, highly efficient, and environmentally friendly separation process for hematite ore. Gravity separation is a clean process that offers advantages such as Parameter Optimization of the Separation Process
احصل على السعر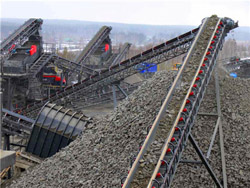
Minerals Free Full-Text A New Route of Roasting-Flotation
The common pre-concentration process for VTM ore is recovering titanium magnetite via low-intensity magnetic separation (LIMS) firstly, and then Nykänen, V. P. et al. True flotation versus entrain-ment in reverse cationic flotation for the concentration of iron ore at industrial scale. Miner. Process. Extract. Biodegradable ether amines for reverse cationic flotation
احصل على السعر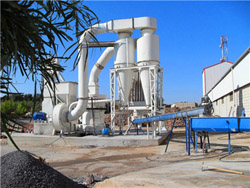
The Role of Water Chemistry in the Concentration of Hematite Ore
The effectiveness of selective flocculation and dispersion processes for the concentration of hematite (Fe2O3) ore are strongly dependent on the ionic content of the Currently, iron is extracted from ores such as hematite by carbothermic reduction. The extraction process includes several unit steps/processes that require large Hematite reduction by hydrogen plasma: Where are we
احصل على السعر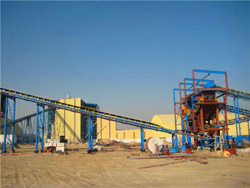
Reduction behavior of hematite ore with different particle
The effects of hematite ore with different particle sizes on the conversion rate, phase, and structural evolution during the SMR process were systematically Based on process mineralogical study of an oolitic hematite ore in SW China, the texture and structure of the ores, the occurrence of iron minerals and the dissemination of them are determined in detail, which provides Process Mineralogy of an Oolitic Hematite Ore
احصل على السعر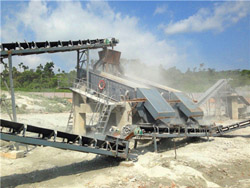
Kinetics of hematite to magnetite transformation by gaseous reduction
Section snippets Initial materials. Hematite ore from Kryvyi Rih iron ore basin (Ukraine) was ground to a particle size <0.07 mm. Afterwards, a magnetic fraction was removed from the ground sample by wet low-intensity magnetic separation at a field of 500 mT.The resulting concentrate consisting of hematite and a trace amount of quartz The kinetic analysis indicated that the reduction of hematite ore to magnetite is a single-step process, which can be described using the first-order reaction model. The reaction rate decreased when exposure time increased. The reaction rate constant increased by more than 20 times with increasing temperature from 300 to 600 °C.Kinetics of hematite to magnetite transformation by gaseous
احصل على السعر
Production of hematite concentrate from low
The experimental results showed that both gravity based separation and high intensity magnetic separation were effective on concentration of low grade hematite ores. A concentrate (-9,53+6,35 mmExtraction of Iron from Hematite 1). Concentration. Hematite is concentrated by the gravity separation process which is a method based on the difference in specific gravities of the metallic ore and gangue particles. The oxide being heavier settles to the bottom while lighter impurities come to the surface and are removed.Extraction of Iron: Meaning, Purification, & Extraction Methods
احصل على السعر
Concentration of Ore Learn Important Terms and Concepts
The concentration method of iron ore is magnetic separation. The powdered magnetite or hematite is subjected to a conveyer belt and when the magnetic roller starts rotating, the iron particles get attracted towards the roller and all other impurities are separated away from it. In the ore iron, the mineral pyrite is found associated with it.The aim of this study was to precipitate goethite from high-iron(II)-bearing atmospheric and heap leach solutions of lateritic nickel ore generated either by reductive leaching of the ore or by reducing Fe(III) of the leach solution to Fe(II) using a suitable reducing agent and to understand the Ni and Co losses during the iron precipitation. Iron Removal as Goethite from Synthetic Laterite Leach
احصل على السعر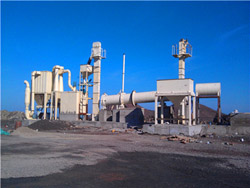
Upgradation of Iron Ore Fines and Slime by Selective
Washing of iron ore fines and slime (10% and 25% w/v, slurry concentrations) with two types of surface-active agents (sodium humate (synthesized) and AD 200 (commercial)) at varying concentrations at pH 8 was conducted for ascertaining the efficacy of dispersants in beneficiating the low-grade iron ores. The beneficiation process The Flowsheet for Hematite Benefication Process by Flotation. The above flowsheet has been developed to produce a high grade product economically with maximum recovery. Due to the flexibility of Units and especially the “Sub-A” Flotation Machine, gravity flow can be utilized throughout the mill, thus keeping pumping requirements to a minimum.Hematite Processing by Flotation 911 Metallurgist
احصل على السعر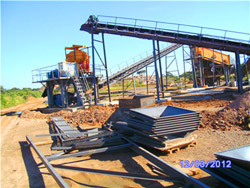
Green hematite depression for reverse selective flotation
The recovery of quartz and hematite did not significantly change till the DDA concentration reached 75 mg/L. Micro-flotation outcomes released that without the addition of LBG, quartz, andAbstract. The role of reagents utilised in iron ores flotation is reviewed. Desliming and flotation stages should be performed at pH levels as low as possible to reduce the expenses with caustic soda. Ether amines are by far the mostly utilised class of collector. The degree of neutralisation of the ether amine is an important process Reagents in iron ores flotation ScienceDirect
احصل على السعر
Characterization and mapping of hematite ore mineral
The study demonstrates a methodology for mapping various hematite ore classes based on their reflectance and absorption spectra, using Hyperion satellite imagery. Substantial validation is carried out, using the spectral feature fitting technique, with the field spectra measured over the Bailadila hill range in Chhattisgarh State in India. The results The hematite conductor concentration changes in the synthetic specimens and accordingly the texture of the specimens. (Sen, 1981; Knight and Endres, 1990; Knight and Nur 1987), or interface reactions (Maxwell–Wagner relaxation process) between grains Hematite is a dense and hard mineral that is the most significant iron Electrical properties of hematite and pure sand synthetic
احصل على السعر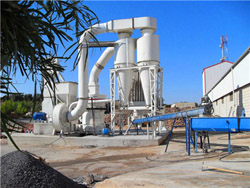
Mineral and Technological Features of Magnetite–Hematite Ores
The magnetite–hematite ores of the Mikhailovskoye deposit are characterized by fine dissemination of ore and gangue minerals, the complexity of the structural and textural features and material composition, a low-level contrast in the magnetic properties of the separated minerals, and so forth. 28−30 The content of iron in 3. Methodology. The purpose of this study is to develop a model for concentrating iron-bearing minerals, mainly magnetite and hematite, from Thanatia until a concentration in equivalent-iron content similar to the one published in the ERC for hematite (Fe 2 O 3) is reached.This indicates a starting concentration of 3.6% iron in Thanatia (x Avoided energy cost of producing minerals: The case of iron ore
احصل على السعر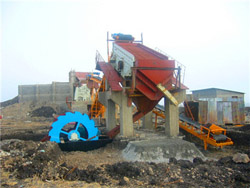
Mineral and Technological Features of Magnetite–Hematite
The BHQ ore was assayed as 38.9wt% Fe, 42.5wt% SiO2, and 1.0wt% Al2O3. In this ore, hematite and quartz are present as the major mineral phases where goethite, martite, and magnetite are present in small amts. The liberation of hematite particles can be enhanced to about 82% by reducing the particle size to below 63 μm.To explore the microstructure evolution of oolitic hematite during microwave fluidization roasting, COMSOL multiphysics and scanning electron microscopy (SEM)–energy-dispersive spectrometry (EDS) were used to simulate and explore the microstructure evolution. The simulation results indicated that with the extension of Study on Microstructure Evolution of Oolitic Hematite during
احصل على السعر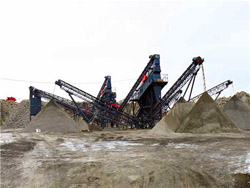
(PDF) Feasibility of Producing Pellet Grade Concentrate by
the iron ore mines producing hematite are provided with washing plants to produce quality lumps (-40+10 mm ) and fines ( -10+0.15 mm) for blast furnace and sintering plant operations.Hematite NPs (α-Fe 2 O 3 NPs) have also attracted attention from the academic and industrial community as they represent one of the most durable forms of iron oxide [168].An extensive literature survey reveals that (α-Fe 2 O 3 NPs) have shown their worth in the elimination of heavy metals such as lead, copper and strontium from the aqueous Hematite an overview ScienceDirect Topics
احصل على السعر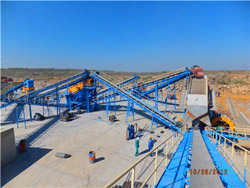
How to Extract Iron from Hematite: Methods and Plants
It is easy to extract iron from this kind of haematite by using gravity separation and magnetic separation. Medium-grained hematite refers to iron ore with an embedded particle size between 0.02 and 2mm. This type of hematite is also relatively easy to select, mainly using gravity separation, magnetic separation and magnetic roasting.Section snippets Materials. Hematite iron ore fines from Barbil region of Odisha having 64% Fe are used for pellets preparation. The particle size distribution of the iron ore fines having the specific gravity 4.8 with Blaine no-2672 cm 2 /gm is used as given in Table 1. The anthracite coal is used to maintain uniform temperature throughout the Effect of additives concentration on pelletization of high grade hematite
احصل على السعر