
grinding using a in cement ball mill
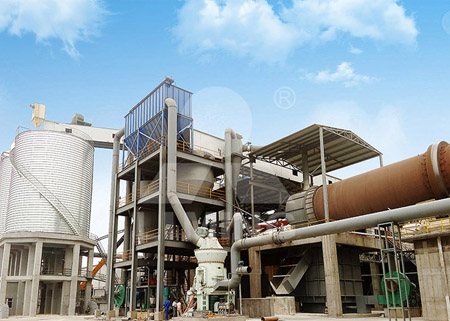
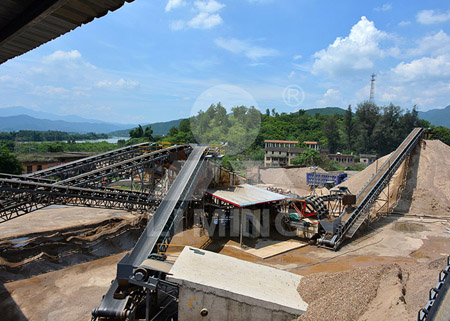
grinding using a in cement ball mill
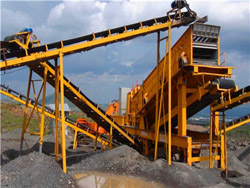
(PDF) Grinding in Ball Mills: Modeling and Process
A ball mill is a type of grinder widely utilized in the process of mechanochemical catalytic degradation. It consists of one or A total of 40% of the total energy consumption of a cement plant is used in clinker grinding in a ball mill to produce the final cement product [ 3 ]. Predictive Controller Design for a Cement Ball Mill
احصل على السعر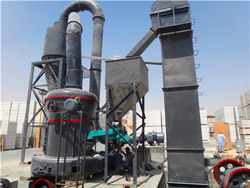
(PDF) Grinding Media in Ball Mills-A Review
A comparison of the grinding media is given together with the knowledge gaps that still need to be bridged to improve the quality and performance of grinding media used in ball mills.Typical specific energy consumption is 30 kWh/t in grinding of cement. Barmac-type crushers found application as a pre Energy-Efficient Technologies in Cement Grinding
احصل على السعر
Energy and exergy analyses for a cement ball mill of a new
Nowadays, ball mills are used widely in cement plants to grind clinker and gypsum to produce cement. In this work, the energy and exergy analyses of a cement Several energy efficient options for cement grinding are available today such as vertical roller mills, roller presses (typically in combination with a ball mill), and clinker pre-grinders with ball mills. Ball mills have been the Optimization of Cement Grinding Operation in
احصل على السعر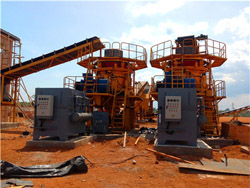
Optimization of a fully air-swept dry grinding cement raw meal ball
• A raw meal ball mill classification circuit was modelled and simulated. • 23% capacity increase could be achieved in cement throughput when pre-drying Within the content of this work, sampling campaigns were organized around a cement grinding circuit and each of the three grinding aids at varying dosage Effects of grinding aids on model parameters of a cement ball mill
احصل على السعر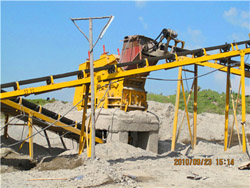
Effects of grinding aids on model parameters of a cement ball mill
In this context, three different types of grinding aids were tested at various dosages in a cement plant and the impacts of grinding aids on model parameters of ball Abstract In fine grinding of cement in a ball mill, it is sometimes impractical to grind finer in a dry state. Even though the chemical reactivity requires the material to be dry ground, it is sometimes [1,2,4], there was significant effect of using grinding aid in cement grinding. Grinding aids are active surface agents that counteract theJournal of Physics: Conference Series PAPER OPEN
احصل على السعر
Cement grinding optimisation ScienceDirect
The efficiency of fine grinding in the second compartment is largely controlled by the size of grinding balls. Due to limitation of the mill’s rotational speed, the smallest ball size is usually restricted to about 15 mm. Cement grinding using stirred mills (Pilevneli and Azizli, 1999) indicates that using smaller media (5–8 mm rangeThe effects of balls and cylinders on the clinker's specific rate of breakage were investigated. The results showed that the specific rate of breakage provided by cylinders is higher than that of balls. − 2.00 + 1.70 mm is an optimum feed size for 20 mm diameter balls and 20 × 20 mm diameter cylinders.At that feed size, the value of Si is The effects of grinding media shapes on the grinding kinetics of cement
احصل على السعر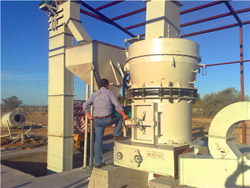
Ball Mill an overview ScienceDirect Topics
Quantum Nanostructures (QDs): An Overview. D. Sumanth Kumar, H.M. Mahesh, in Synthesis of Inorganic Nanomaterials, 2018 3.6.1.1 Ball Milling. A ball mill is a type of grinder used to grind and blend bulk material into QDs/nanosize using different sized balls. The working principle is simple; impact and attrition size reduction take place as the ball After exiting the cement kiln, the clinker is cooled and stored. To produce cement, clinker is mixed with a small amount of gypsum and other additives, such as pozzolans or slag. This mixture is then ground in the cement ball mill. The grinding process involves passing the clinker and additives through the rotating drum of the ball mill, whereWhat Are the Parts of a Cement Mills? Cement Ball Mill
احصل على السعر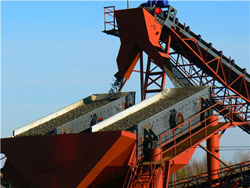
A cement Vertical Roller Mill modeling based on the
Vertical roller mills (VRM) are widely used to grind, dry, and select powders from various materials in the cement, electric power, metallurgical, chemical, and nonmetallic ore industries. For the sectors above, the VRM is a powerful and energy-intensive grinding field [1], [2]. It is used to grind slag, nonmetallic ore, and other block Experiments and simulation results in a laboratory-scale planetary ball mill verify that the particle wear model can predict the increasing trend of particle wear rate with mill speed, and has good accuracy at high mill speed. In the experiments, the grinding bowl is filled with liquid water to isolate the air and cool the grinding balls, andInvestigation of the ball wear in a planetary mill by DEM
احصل على السعر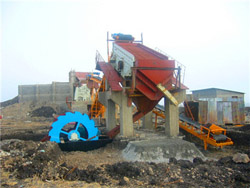
How does a raw mill work in a cement plant? LinkedIn
A raw mill is a key piece of equipment used in a cement plant to grind raw materials into a fine powder. It works by crushing and grinding materials such as limestone, clay, and iron ore into aThe use of grinding aids in stirred mills has also been the subject of many investigations and consequently, it was stated that the use of GA in the stirred mills increased the grinding efficiency and reduced the specific energy consumption [15], [16]. Experimental residence time distribution data for a full-scale cement ball mill wasEffects of grinding aid dosage on circuit performance and cement
احصل على السعر
OPTIMIZATION OF CEMENT GRINDING OPERATION IN
Operation and Elements of a Closed-Circuit Ball Mill System . Cement ball mills typically have two grinding chambers. The first chamber is filled with larger diameter grinding media andlined with lifting liners . The first chamber coarse-grinds the feed material and prepares it for the second chamber. The second chamber is the fine grindingMill feeding increasing together with acceleration wear for Balls, Table (2) diaphragm and the linings (mill interior parts) It is well-known fact when using grinding aid in cement ball mills the feeding increase above the designed mill feeding capacity of the mill which means it can have 100 t/h cement ball and using grinding aid feeding`Grinding Aid Effectiveness in Cement Ball Mill Academia.edu
احصل على السعر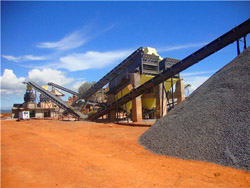
Predictive Controller Design for a Cement Ball Mill
The annual cement consumption in the world is around 1.7 billion tonnes and is increasing by 1% every year [].Cement industries consume 5% of the total industrial energy utilised in the world [].A total of 40% of the total In our study, we use the discrete element numerical modelling (DEM) tool to see if ball segregation can be achieved in a tube mill by simply using appropriate liner profiles. Liners/lifters are known to have strong influence on the load trajectory and ultimately breakage efficiency of the mill (Toor et al., 2013).Using DEM to investigate how shell liner can induce ball
احصل على السعر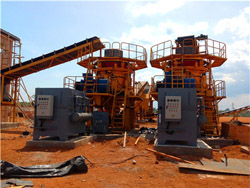
Ball Mill In Cement Plant Cement Ball Mill AGICO Cement
AGICO Cement is a cement equipment manufacturer with more than 20 years’ experience. We are the long-term partner of many large and medium-sized cement enterprises in different countries, providing cement equipment and EPC project construction. The closed-circuit grinding system ball mill for cement grinding and the matching powderCement grinding with our highly efficient ball mill. An inefficient ball mill is a major expense and could even cost you product quality. The best ball mills enable you to achieve the desired fineness quickly and efficiently, with minimum energy expenditure and low maintenance. With more than 4000 references worldwide, the FLSmidth ball mill isBall mill for cement grinding FLSmidth
احصل على السعر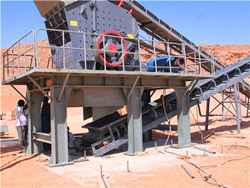
Experimental study on the grinding rate constant of solid materials
Abstract. The grinding rate constant, in the widely accepted first-order expression of grinding rate, is one of the important factors required to evaluate a grinding process particularly for its initial grinding stage of various mill types. In this study, we conducted grinding tests on silica glass, limestone and gypsum using a laboratory ballClinker grinding technology is the most energy-intensive process in cement manufacturing. Traditionally, it was treated as "low on technology" and "high on energy" as grinding circuits use more than 60 per cent of total energy consumed and account for most of the manufacturing cost. Since the increasing energy cost started burning the benefits Clinker grinding technology in cement manufacturing
احصل على السعر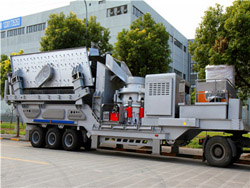
Simulation of clinker grinding circuits of cement plant based
BENZER H. Modeling and simulation of a fully air swept ball mill in a raw material grinding circuit [J]. Powder Technology, 2005, 150: 145–154. KAYNAK O. Neural network modeling and control of cement mills using a variable structure systems theory based on-line learning mechanism [J]. Journal of Process Control, 2004, 14(5): 581–589.Abstract The results of industrial tests of ShKh15steel grinding balls with diameters of 25, 30, and 35 mm of 5th hardness group as per GOST (State Standard) 7524–2015 at AO Kharkiv Pilot Cement Plant during grinding of cement in the second chamber of a cement mill are presented. It is shown that the use of ShKh15 steel Efficiency of Using Small Diameter Grinding Balls for Cement Grinding
احصل على السعر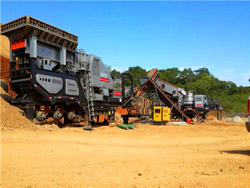
Effect of Grinding Media Size on Ferronickel Slag Ball Milling
The aim of this study is to evaluate the effect that the size of grinding media exerts on ferronickel slag milling efficiency and energy savings. A series of tests were performed in a laboratory ball mill using (i) three loads of single size media, i.e., 40, 25.4, and 12.7 mm and (ii) a mixed load of balls with varying sizes. In order to simulate the
احصل على السعر