
iron ore sizing plant
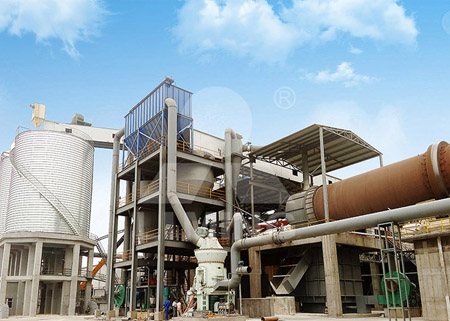
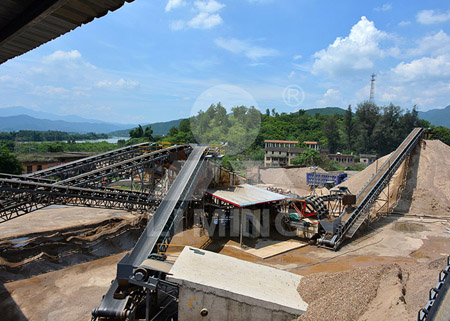
iron ore sizing plant

Introduction: Overview of the global iron ore industry
This chapter first provides an overview of world iron ore production and trade, as well as reserves and resources, followed by a summary of the key mining In order to study in depth the differences in basic characteristics between iron ore fines commonly used by a steel company, and guide the sintering performance plant to choose the best ore Study on the Basic Characteristics of Iron Ore
احصل على السعر
Integrated Production and Distribution Planning for the
ore concentrate is transported from distribution center k to customer s at time t ; constraints () are the demand fulllmentconstraints;constraints()and()aretherangeFernando S. Lameiras Abstract and Figures Currently, approximately 1.4 billion tons per year of iron ore tailing wastes (IOT) are generated, mainly in Australia, (PDF) Iron Ore Tailings: Characterization and Applications
احصل على السعر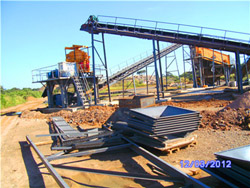
A compact pelletizing plant for iron-ore processing
A compact pelletizing plant for iron-ore processing. This company has optimized its existing induration technology, offering and launched its Compact-sized EXPANSION AND MODERNIZATION OF AN IRON ORE PELLETIZING PLANT IN NORTHERN SWEDEN M. Ahrens, ABB Switzerland, Baden-Dattwil, EXPANSION AND MODERNIZATION OF AN IRON ORE
احصل على السعر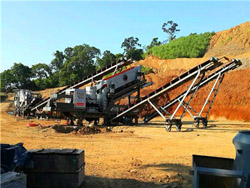
Iron ore beneficiation: an overview ScienceDirect
More than 85% of the hematite ore reserves are of medium- to high-grade (+62% Fe) and are directly used in blast furnace and in direct-reduced iron (DRI) plants Like other sintering processes, iron ore sintering converts iron ore fines of often − 8 mm sizing into larger agglomerates, namely, sinter, between 5 and 50 mm Iron ore sintering ScienceDirect
احصل على السعر
Recycling and Reuse of Iron Ore Pellet Fines SpringerLink
During the process of iron ore pelletization and preparation of feed for DRI or reduction smelting processes, around 3% of pellet fines (less than 8 mm) are generated as undesired product in the existing pellet plants. Such pellet fines acquire more than 24 million tonnes generated all over the world. Recycling and reuse of these high gradebut more iron ore powder particles of larger size. To avoid differences in the sintering properties of the same iron ore powder due to different particle sizes, this study carried out the assimilation, liquid phase fluidity indices, and binding phase strengths of several iron ore powders commonly used in a steel mill with different particle sizes.Study on the Basic Characteristics of Iron Ore Powder
احصل على السعر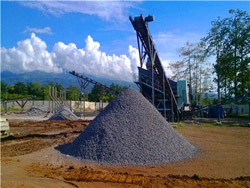
Improved iron recovery from low-grade iron ore by efficient
The requirement for iron ore is increasing with the rapid development of industry. Therefore, it is necessary to develop a method for the high utilization of high-phosphorus limonite. Traditional processes can't treat low-grade iron ore and are unable to transform the phase of iron minerals, thus they are very inefficient.Bazin et al. (2014) have reported mineral size recovery curves of roughing, cleaning, and re-cleaning spirals at two Canadian iron ore processing plants. It was noted that rougher, cleaner and re(PDF) Size recovery curves of minerals in industrial spirals for
احصل على السعر
Iron ore sintering ScienceDirect
Like other sintering processes, iron ore sintering converts iron ore fines of often − 8 mm sizing into larger agglomerates, namely, sinter, between 5 and 50 mm particle size, which possess the physical and metallurgical characteristics and gas permeability required for efficient blast furnace operation.As shown in Figure 14.1, iron ore sintering is In order to study in depth the differences in basic characteristics between iron ore fines commonly used by a steel company, and guide the sintering performance plant to choose the best ore allocation method, experimental studies on the basic characteristics of seven iron ore powders of three sizes were carried out using micro-sintering Study on the Basic Characteristics of Iron Ore Powder with
احصل على السعر
Integrated Production and Distribution Planning for the
ore concentrate is transported from distribution center k to customer s at time t ; constraints () are the demand fulllmentconstraints;constraints()and()aretherangeMineral Processing Plants. Whatever minerals you process, wherever your operation may be, Multotec will help ensure your mineral processing plant is optimised to deliver the lowest cost per ton. From individualised equipment to complete plants greenfield or retrofit our engineers and metallurgists will work with you to achieve yourMineral Processing Plants Multotec
احصل على السعر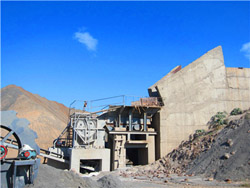
Influence of Iron Ore Fines Feed Size on Microstructure,
JSW Steel sinter plant receives iron ore fines of –10 mm size from Bellary Hospet region which consist of 3 to 9% bigger than 10 mm and Various researchers define the sizes of the nucleus and adhering particles differently. According to Bergstrand et al. the nucleus forming particles are +1 mm, while the adheringBy contrast, concentrations of Si in iron ores played a significant role in decreasing PCDD/F and PCB emissions in both sinter and dust samples. This study also confirmed the optimum size (< 1 mmInfluence of iron ore properties on dioxin emissions during iron ore
احصل على السعر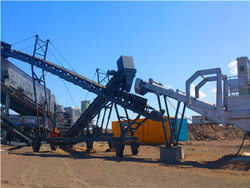
Iron ore pellets as a solution to steel—making raw Springer
The excessive fines generated from the iron ore mining and crushing units for sizing the feed for blast furnace and sponge iron ore plants are mostly un-utilised. Monnet Ispat & Energy Ltd is setting up a 2.2-Mt/a iron ore pellet plant in Raigarh to meet the requirements its first steel plant of 1.5 Mt capacity in Chhattisgarh's RaigarhIron ores are rocks and minerals from which metallic iron can be extracted. There are four main types of iron ore deposit: massive hematite, which is the most commonly mined, magnetite, titanomagnetite, and pisolitic ironstone. These ores vary in colour from dark grey, through to deep purple, rusty red and bright yellow.Iron ore BHP
احصل على السعر
Iron Ore Pelletization: Part I. Fundamentals
The behavior of iron ore pellet binders is complex. Any pellet binder is subject to a handful of practical requirements: that it be readily dispersed through a pellet, that it effectively controls the movement of water within the pellet, and that it contributes to the inter-particle bonding within the pellet.Iron (Fe) is a metallic element that constitutes 5.6% by weight of the Earth's crust and is the fourth most abundant element in the crust. Iron ores are rocks from which metallic iron can be economically extracted. The principal iron ores contain hematite (Fe 2 O 3) and magnetite (Fe 3 O 4 ). Hematite is an iron oxide mineral.Iron Ore Geoscience Australia
احصل على السعر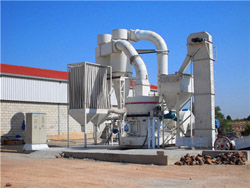
Investigation on Iron Ore Grinding based on Particle Size Distribution
The feed samples of X, Y, and Z iron ores were ground in the BBM (ball mill refers to a BBM of size 300 mm × 300 mm with smooth liners) to identify the PSD, BWI, and RT of each ore. Grinding experiments were conducted according to Bond’s standard test procedure [].For each iron ore sample, the RT taken to produce 250% circulating In order to study in depth the differences in basic characteristics between iron ore fines commonly used by a steel company, and guide the sintering performance plant to choose the best ore allocation method, experimental studies on the basic characteristics of seven iron ore powders of three sizes were carried out using micro-sintering equipment, mainly Study on the Basic Characteristics of Iron Ore Powder with
احصل على السعر
Direct Reduced Iron By-Product Fines (DRI D): A Guide
iron ore during the reduction process and this dust is carried off with the offgas and has to be separated from the gas stream via the off-gas scrubber(s). site pelletising or briquetting plant if one exists, or sold to third parties. DRI Fines component Total Fe % Metallic Fe% Carbon % Gangue % Moisture % Metallised DRI Fines 80 90 1 Scope. This International Standard gives the definitions for terms used in TC 102 standards for sampling, sample preparation, moisture and particle size analysis and physical testing of iron ore and direct reduced iron. Some specific analytical terms used in the relevant International Standards are also included.ISO 11323:2010(en), Iron ore and direct reduced iron
احصل على السعر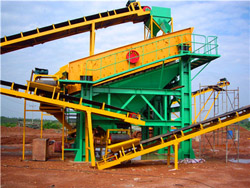
Effect of Iron Ore Pellet Size on Metallurgical Properties
Iron ore pellets are small and hard spherical particles agglomerated from a fine iron ore concentrate. They are used in the blast furnace process to produce hot metal. The diameter of blast furnace pellets is usually between 8 and 16 mm. In this study, a batch of magnesia iron ore pellets was first sieved into particle sizes of 8–10 mm, 10–12.7 mm, Methods to evaluate the liberation characteristics of an iron ore feed in a jigging plant have been given by Mukherjee et al. (2008). Das et al. (2007) studied the beneficiation of a low-grade(PDF) Effective Beneficiation of Low Grade Iron Ore
احصل على السعر