
cost of construction of cement coal mill
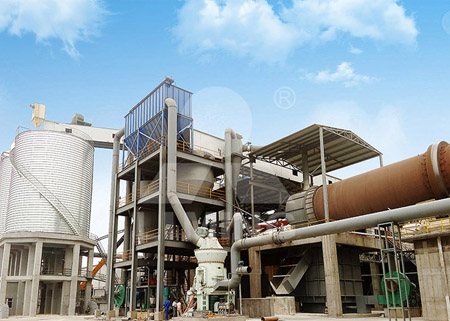
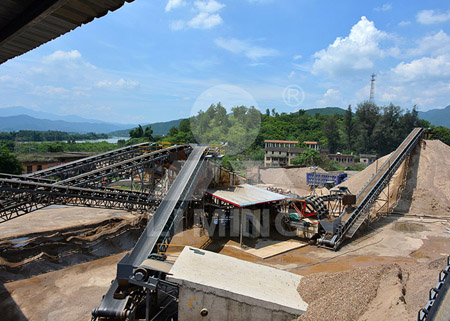
cost of construction of cement coal mill
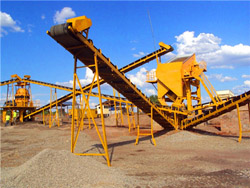
Coal utilization in the cement and concrete industries
Coal combustion products in the form of bottom ash and fly ash derived from the use of coal in power stations is a significant element in coal’s role in the cement [Coal Mill In Cement Plant Maintenance Manual][PRICE, Cement Mill,Cement Coal Mill,Cement Processing Equipment Sale. Cement Coal and Mill Equipment Costs cost of construction of cement coal mill shibang-china
احصل على السعر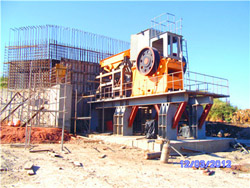
Frontiers Evaluating the Carbon Footprint of Cement Plants
The results of the analysis were compared to a conventional cement production process. The results show that the GHG emissions may be reduced by 74% with a tail-end In the study the advantages of vertical roller mill are discussed over ball mills. VRM construction, its process and parameters which affects the performance and Review on vertical roller mill in cement industry & its
احصل على السعر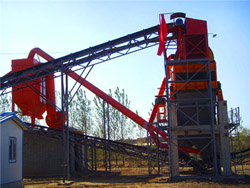
Towards a business case for CO2 mineralisation in the cement
The implementation of CCU M creates a profit of approximately €129t SCMccu−1 (direct) and €117t SCMccu−1 (indirect) leading to additional profit of €44 M Based on the results of tensile strength tests and estimating the cost of concrete construction, the highest ratio of tensile strength to cost was obtained by using Optimizing the tensile strength of concrete containing coal
احصل على السعر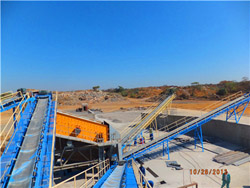
Optimizing the tensile strength of concrete containing
(–%)on the tensile strength to cost of concrete construction were evaluated. Presenting the model, optimizing and investigating the individual, reciprocal The Study Offers a Detailed Cost Analysis of Cement Production Process From Limestone, Sand, Clay, and Bauxite. In Addition, the Report Incorporates the Manufacturing Process Cement Production Cost Analysis Reports 2023
احصل على السعر
Deep decarbonisation of industry: The cement sector
2017, equivalent to a reduction in cement per capita from 0.5 to 0.3 tonnes per person (3). The CO 2 intensity of cement production over that period has improved by about 7% (0.6t of CO 2 emitted per tonne of cement in 2017) (2). By 2050, cement production in the EU is expected to remain below pre-2010 levels, ranging between 165MtInstitute of Building Materials Industry. CSIBM. As shown in Fig. 10, energy efficiency plays a key role in reducing future energy consumption in China’s cement industry. The cost-effective energy saving potential amounts to 427 PJ in 2015, 865 PJ in 2020, 1367 PJ in 2025, and 1910 PJ in 2030, respectively. coal mill and cement millEvaluating co-benefits of energy efficiency and air
احصل على السعر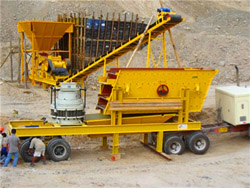
Reducing energy consumption of a raw mill in cement industry
While total electrical energy consumption for cement production is about 100 kWh/ton of cement, roughly two thirds are used for particle size reduction [2]. About 65% of the total electrical energy used in a cement plant is utilized for the grinding of coal, raw materials and clinker Fig. 1. The cement industry one of the worst pollutantImproving Energy Efficiency: Cement industry steps up its efforts. May 14, 2020. India is the second largest producer of cement in the world. At present, the installed capacity of cement in the country is 540 million tonnes per annum (mtpa), with production at 298 mtpa. With the increase in the growth of infrastructure, cement production inImproving Energy Efficiency: Cement industry steps up its
احصل على السعر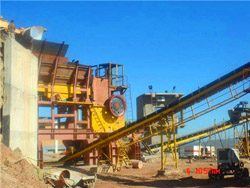
en/cement factory coal mill system test.md at main lbsid/en
Quality Assurance of Cement from Production to Construction. Very accurate : For Coal,Cement Additives Dosing Limestone Clay,Flyash Typical Close Circuit Raw Grinding with High Efficiency Separator Homo Silo Si Fe Raw mill High Efficiency Separator Product XRF analyzer Belt analyzer KilnFeed RawMixController.coal mill in cement VRM has been widely researched in processing of cement (Ito et al. 1997;Jorgensen 2005;Wang et al. 2009, Ghalandari et al. 2021), coal (Tontu 2020), iron ore (Reichert et al. 2015), zinc ore (vanAn investigation of performance characteristics and
احصل على السعر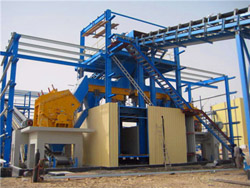
Optimizing the tensile strength of concrete containing
cost of concrete by RSM were conducted for the ˜rst time. Based on the results of tensile strength tests and estimating the cost of concrete construction, the highest ratio of tensile strength to cost was obtained by using the cement content of 340˛kg/m 3, water/cement of 0.45, gravel v%oal wast%n this case, the response value wasCement industry is estimated to account for ~6–7% of anthropogenic CO2 emissions globally. Therefore, the identification of innovative solutions for their mitigation is both a priority and a challenge. The integration of carbon capture and storage technologies into the industrial production process is considered among the most viable solutions for this Frontiers Evaluating the Carbon Footprint of Cement Plants
احصل على السعر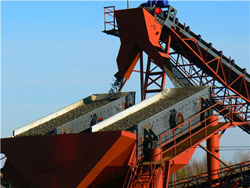
Milling Cost an overview ScienceDirect Topics
Pulverized-coal firing is especially suitable for very large boilers and cement kilns. A wide range of coals can be burnt, but coal preparation and gas cleaning are major cost items. 70% < 75 μm is required for bituminous coals, 80% for anthracite. Coal dried with air at 250–350°C for milling in low-, medium- or high-speed mills.Cement emissions intensity has remained relatively stable since 2018, at just under 0.6 t CO 2 per tonne of cement produced, following several years of modest increase largely due to an increasing clinker-to-cement ratio in China. To get on track with the NZE Scenario, emissions must fall by an average of 3% annually through to 2030.Cement IEA International Energy Agency
احصل على السعر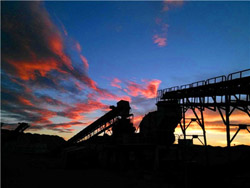
Integrated energy optimisation for the cement industry: A
Energy costs play a major role in the cement production process. As much as 60% of total cost is allocated to energy and 18% to the consumption of electrical energy. Historically, energy cost savings were achieved by large infrastructure upgrades. These upgrades are often costly and lead to interruptions in production.In China, the cement plants use coal as fossil fuels in the burning or incineration process (CBMA, 2011). The coal is ground by mill and then is put into the calciner and kiln. Čuček et al., 2011, Čuček et al., 2012c) have done the life cycle assessment study and optimization analysis of regional biomass and bio-energy supply The life cycle inventory study of cement manufacture in China
احصل على السعر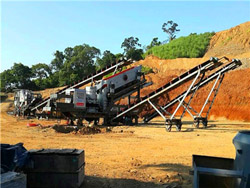
Methodological development for the optimisation of electricity cost
Cement factories require large amounts of energy. 70% of the variable cost goes to energy—33% to kiln thermal energy and 37% to electrical energy. This paper represents the second stage of a broader research study which aims at optimising electricity cost in a cement factory by means of using artificial intelligence. After an analysis of the The fly ash is widely used as cement supplementary cementitious material in concrete. Initially fly ash was used in the ranges of 15% to 25% by mass of the cementitious material component in concrete. The recent research studies have shown that concrete with good strength and durability properties can be made with using high volumes of fly ash.Sustainable Concrete Made with Ashes and Dust from
احصل على السعر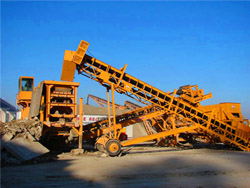
Quantifying co-benefit potentials in the Chinese cement
The cement industry has a pivotal role in CO 2 emissions. In the current technology level, the average heat consumption for cement production is 110 kgce (kg coal equivalent) for per ton of cement production, and the average power consumption is 110 kWh for per ton of cement produced. This average is much higher than the international Concrete is used worldwide as a building material and is the most consumed substance on Earth after water (coal mill) 6-29NO16D: 50,000 m 3 /h: Cement grinding: 7: V-separator: HFV350: 180,000–240,000 m 3 /h: understanding of how recycling the low-temperature waste gas in various applications would affect the Analysis of material flow and consumption in cement
احصل على السعر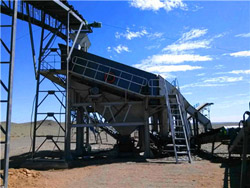
Energy consumption assessment in a cement production plant
The process of manufacturing cement is known to be an energy-intensive process; it involves the consumption of coal (fossil fuel), electrical energy, as well as other resources of energy, and thisCoal is used as an energy source in cement production, which is a critical commodity for the construction industry. Over 3.3 billion tonnes of cement were consumed globally in 2010. Cement is made from a mixture of calcium carbonate, silica, iron oxide and alumina in a high-temperature kiln that is often fuelled by coal.Industrial uses of coal ScienceDirect
احصل على السعر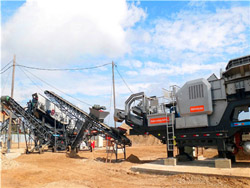
Is Carbon Capture and Storage (CCS) Really So Expensive?
Carbon capture and storage (CCS) is an essential technology to mitigate global CO2 emissions from power and industry sectors. Despite the increasing recognition of its importance to achieve the net-zero target, current CCS deployment is far behind targeted ambitions. A key reason is that CCS is often perceived as too expensive. The costs of The cement production process begins with the extraction of limestone and clay from the quarry. The material is then blended, crushed and fed to the kiln. Post-kiln, the clinker is cooled and goes through a final grinding method before it is ready to ship. Portland cement, the most common type of cement, is formulated in a variety of strengthsCement Analysis and Production Information Thermo
احصل على السعر