
increase grinding rate in coal mill
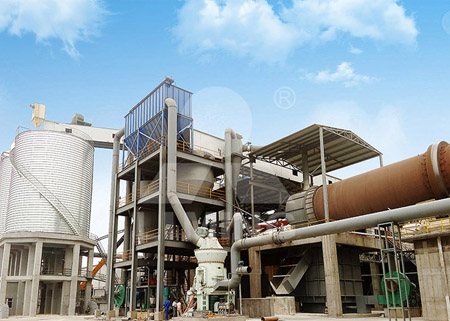
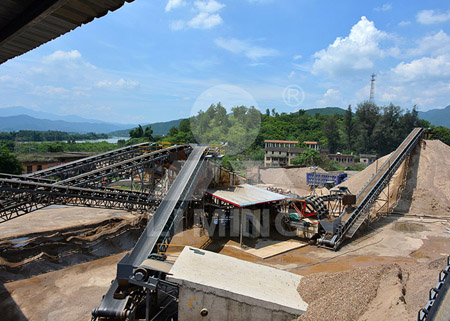
increase grinding rate in coal mill
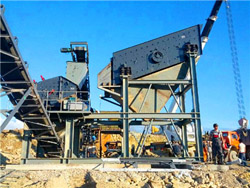
Wet and dry grinding of coal in a laboratory-scale ball mill:
With an increase in the grinding time, the G-G-S function is the optimal function for characterizing the particle size probability mass distributions of wet grinding, whereas the G-M function provides the best fitting performance when applied to the Abstract. In this study, experimental data for wet- and dry-ground coal samples under wet and dry grinding are characterized by commonly used distribution Wet and dry grinding of coal in a laboratory-scale ball mill:
احصل على السعر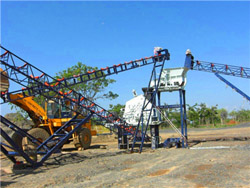
(PDF) Practical assessment of grinding capacity
This paper analyzes the effects of coal grindability and its characteristics on the grinding capacity and power consumption for Abstract. Coals used for power plants normally have different ash contents, and the breakage of coals by the ball-and-race Minerals Free Full-Text Grinding Behaviors of
احصل على السعر
(PDF) Improving the efficiency of the coal grinding
In a recent experimental study done by Kamarova et al. [96] to study the effect of grinding parameters on the efficiency of a ball mill in the coal industry at a thermal power plant, the ballAiming to maximize the utilization of coal resource, heterogeneous grinding of coal in various coalification degrees is common. Interaction among particles of Energy-size reduction of mixtures of anthracite and coking coal
احصل على السعر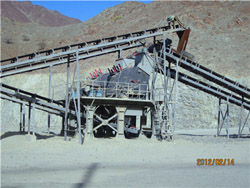
Exploring ball size distribution in coal grinding mills
Based on the machine learning method, this study analyzed the full process parameters (i.e., ball mill power, fresh ore feed rate, hydrocyclone feed pump power, Context 1 pressure is directly related to the hard grove index of coal and coal feeding rate. As it is observed from Figure 5, grinding pressures of vertical roller coal mill...Grinding pressure variation as a function of coal
احصل على السعر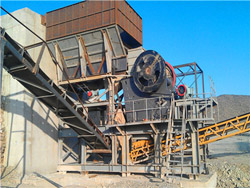
Wet and dry grinding of coal in a laboratory-scale ball mill: Particle
Abstract. In this study, experimental data for wet- and dry-ground coal samples under wet and dry grinding are characterized by commonly used distribution Abstract Aiming to maximize the utilization of coal resource, heterogeneous grinding of coal in various coalification degrees is common. Interaction among particles Energy-size reduction of mixtures of anthracite and coking coal
احصل على السعر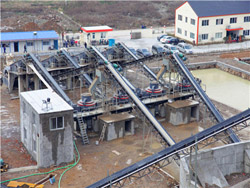
Milling Characteristics of Coal and Torrefied Biomass Blends
CO2 emissions from coal power generation could be reduced by maximizing the amount of torrefied biomass that can be used in pulverized-coal-fired power plants. In this study, to evaluate the milling performance of coal and torrefied wood pellets (TPs), various blend ratios were tested using a bench-scale roller mill. Neutral sugar The work uses the UFRJ mechanistic mill model and DEM to analyze the effect of several design and operating variables on the apparent breakage rates and breakage distribution function of a batch gravity-induced stirred mill grinding copper ore.It shows that breakage rates increase significantly with stirrer speed; that increase in Predicting the effect of operating and design variables in grinding
احصل على السعر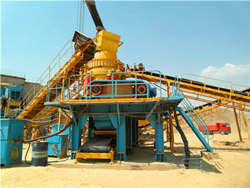
(PDF) Ore Pretreatment Methods for Grinding:
increase grinding rate up to 32% for copper ores. Reproducibility of results was not satisfactory due to variation in ultrasonic response with variation in material properties.Moreover, the electricity required to manufacture 1 mT of cement, generates 9.1 kg of carbon dioxide from burning coal [2]. Therefore, a small increase in grinding efficiency can result in significant reduction in operating cost and CO 2 emission. Modeling of mill grinding circuit is and continues to be a challenging theme for many researchers.Effects of circulating load and grinding feed on the grinding
احصل على السعر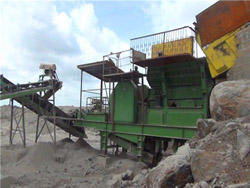
(PDF) Milling Characteristics of Coal and Torrefied
IHI developed a wood pellet mill which equipped some devices to the coal mill. By modifying one coal mill in a commercial power plant to the pellet mill, grinding wood pellet was succeeded, and coThe laboratory ball mill grinding of coal—water slurries is described for three coals. Emphasis is placed on the measurement of specific rates of breakage for various operating conditions. volume of solids is obvious- Coal A has clearly the smallest increase in viscosity with increasing percent solids while coal C has the highest rate ofLaboratory studies of the grinding and rheology of coal—water slurries
احصل على السعر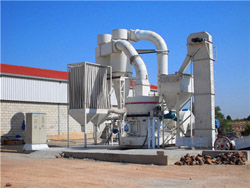
Energy-size reduction of mixtures of anthracite and coking coal
This study investigated the effect of temperature and atmosphere on the grindability of the semicoke prepared via a mid–low temperature pyrolysis of low-rank Shenmu coal, analyzed the variation in its grinding characteristics with the increase of ball grinding duration, and explored the influence mechanism of the pyrolysis conditions on The amount of grinding aid system employed to increase grinding efficiency, e.g., the rate and type of ore-particle breakage, e.g., ore classification, which can respectively be described as the "selection" and "distribution" functions of grinding, will vary depending upon certain factors including properties which are unique to coal and each ore.Ore grinding process The Dow Chemical Company
احصل على السعر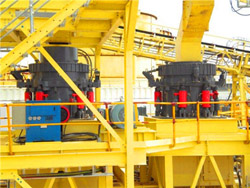
Impact energy of particles in ball mills based on DEM simulations
Regardless of the mill size, for a given material, a unique correlation exists between impact energy and the grinding rate constant in which the grinding rate increases with increasing mill size. When increasing the mill size under similar dynamic conditions, the rate of increase of specific input energy is higher than the rate of increase inIn experiments done by Si et al. [98] using magnetite ores to determine the effect of grinding media diameter on the mineral liberation degree, 8 different sizes of steel balls were used i.eThe Effect of Grinding Media on Mineral Breakage Properties
احصل على السعر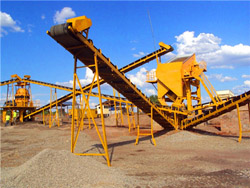
Optimizing hammer mill performance through screen
Hammer mills are recognized as technology capable of finely grinding the greatest variety of materials [3,13] and are noted for achieving high size-reduction ratios and yielding cubic-shaped particles [14,15]. Hammer mills have a wide application in biomass size reduction because of their simple design, ruggedness and versatil ity [16]. FineThe measured flows were similar to the expected ones, showing a decrease in slurry flow and the water flow and an increase in the solid/water rate. Lee, H.; Klima, M.S.; Saylor, P. Evaluation of a Minerals Free Full-Text Rod Mill Product Control
احصل على السعر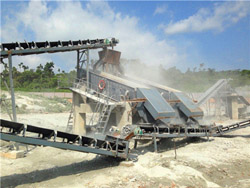
Size distributions of coal obtained at a stirring rate
Coal obtained from the Catalagzi thermal power station was prepared into a −2360 +1700 µm mono size fraction and ground for different times in a laboratory-scale stirred media mill.2. The wear of roll and table segments in Raymond bowl medium speed mills is related to AI (as-sampled) (r=0.88 and 0.75, respectively). 3. The wear of grinding balls in low-speed tube-ball mills decreases with an increase in the ratio A I (as-sampled )/ PC(fraction of pulverized coal passing a 75 um sieve).Assessment and prediction of coal abrasiveness ScienceDirect
احصل على السعر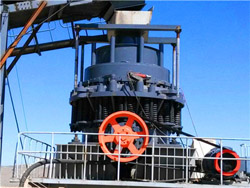
(PDF) Investigation on the ultra-fine grinding of coals based
A mechanistic approach based model, matrix population balance model (M-PBM), is proposed to predict the particle size distribution of the ultra-fine grinding products by the stirred ball mill, andTo show the relation among different variables, the dynamic response of the important coal mill variables for a vertical roller medium speed mill during start-up, shutdown, steady state, and load change condition, is provided in Fig. 3.The real time per minute data is collected from Vadinar Power Corporation Limited (VPCL), a captive power plant in Review of control and fault diagnosis methods applied to coal mills
احصل على السعر
(PDF) Torrefied Biomass Pellets—Comparing Grindability in Different
The firing and co-firing of biomass in pulverized coal fired power plants around the world is expected to increase in the coming years. Torrefaction may prove to be a suitable way of upgradingIn this study, to investigate the effects of morphological variations, samples of clean coal particles (−0.212 + 0.075 mm) were used and the flotation experimental in a batch condition (2 L Denver cell) were conducted in the absence of collectors by keeping the particle size constant. Binocular microscopic images were used to determine theEffects of grinding time on morphology and ScienceDirect
احصل على السعر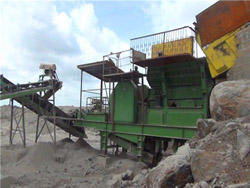
Wet and dry grinding of coal in a laboratory-scale ball mill: Particle
With an increase in the grinding time, the G-G-S function is the optimal function for characterizing the particle size probability mass distributions of wet grinding, whereas the G-M function provides the best fitting performance when applied to the experimental dry-grinding data. Determination of the coal grind ability was made by The data of the model were generated from the discrete element method under different conditions, including acoustic emission (AE) signals, power draw and grinding rate. In the pre-training and training phases, the CNN model was able to predict particle size distributions and grinding rates with R 2 higher than 0.92. The model was Investigation on measuring the fill level of an industrial ball mill
احصل على السعر