
grinding in production of ceramic powder
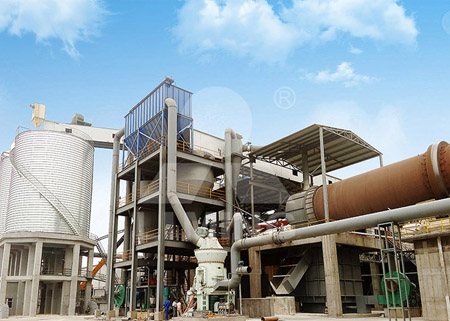
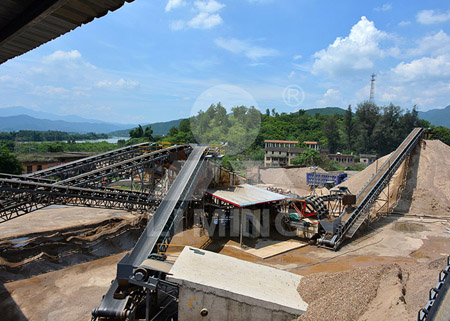
grinding in production of ceramic powder

(PDF) On the Use of Ball Milling for the Production
PDF In the present research work the mixture of boron carbide and graphite ceramic powders with a theoretical composition of Request PDF Powder Mixing and Grinding Processes for Ceramics This article describes the best conditions to grind ceramic powders while limiting Powder Mixing and Grinding Processes for Ceramics
احصل على السعر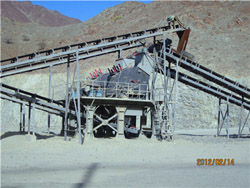
Process of fine milling for ceramic materials ScienceDirect
The production of very fine powders can be achieved by using modern grinding machines, e.g. stirred ball mills and vibration mills for wet grind- ing or jet mills Ceramic Powder Production. Advanced ceramic applications require specific microstructural characteristics: small defect size, homogeneous dispersion of the Powder Processing of Bulk Components in Manufacturing
احصل على السعر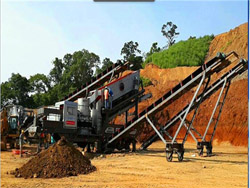
Dry pressing of ceramic powders SpringerLink
Quinn, D.B., Bedford, R.E. and Kennard, F.L. (1984) Dry-bag isostatic pressing and contour grinding of technical ceramics, in Advances in Ceramics, Vol. 9, Forming of Ceramics (eds J.A. Mangels and G.L. Grinding Powder ceramic Particle modification Mechanical activation Particle size 1. Introduction Porous ceramics are considered an important class of Mechanical treatments on design powder ceramic materials:
احصل على السعر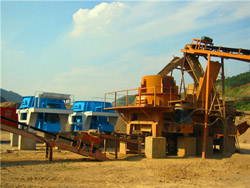
Wet vs Dry Processing: Granulation of Ceramic Powders
This paper will follow a literature survey approach, along with reference to personal industrial experience, to evaluate the different methods of preparing ceramic powders for dry Abstract. The use of ceramic beads as grinding media within high intensity stirred mills (such as the IsaMill) is desirable to maximise the energy efficiency Improving The Efficiency Of Fine Grinding
احصل على السعر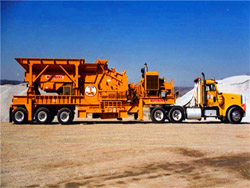
Fundamentals of Ceramic Powder Processing and Synthesis
It covers the three reactant processes used in synthetic ceramic powder synthesis: solid, liquid, andgas.Ceramic powder processing, as a field of materials processing, is 2 CERAMIC GRINDING MEDIA OVERVIEW Two manufacturing processes may be distinguished in the production of ceramic media commonly used in fine grinding for non-contaminating applications: • Sintered ceramic beads obtained by a cold forming of ceramic powder and by firing in high temperature kilns.Improving The Efficiency Of Fine Grinding
احصل على السعر
Powder Metallurgy SpringerLink
3.1 Introduction. Powder metallurgy (PM) is a processing technique for the synthesis of alloys and composites. This chapter includes the study of conventional routes of powder metallurgy, as well as unconventional techniques based on powder manipulation through mechanical alloying (MA). The most common elements used in the production of It is crucial to study how ceramic ball grinding affects the production of tiny particles in powders. Comparing the experimental findings with the information gained from the well-researched steel ball grinding procedure is a great technique to assess the impact of the ceramic ball grinding process on the characteristics of magnetite powderEffect on Fine Particles Output Characteristics of Ceramic Ball Grinding
احصل على السعر
Ceramics Free Full-Text Chemical Preparation Routes and Lowering
Standard methods for powder production are mechanical, using a roller crusher, roller mill or ball mill. The corresponding average grain sizes are typically close to mm, or ten to a few µm, respectively [15,16,41,42]. The grinding is necessarily associated with pollution by the wear of the grinding agents (quartz pebbles, metal balls, andDry or wet grinding, steel ball size or shape, feed particle size, grinding concentration, grinding time, filling ratio, rotational rate and other operating conditions will also significantlyInfluence of dry and wet grinding conditions on fineness and
احصل على السعر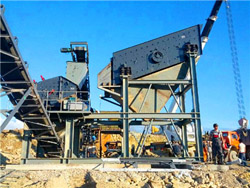
Ceramics Process Engineering ScienceDirect
Process engineering of ceramics is a practical discipline, many of its procedures being based on empirical rather than strictly scientific relations. Lack of sufficient characterization, particularly of powder properties, adds to the complexity of the ceramics process with its many individual steps, making a description of processing by way ofThe hybrid reactions of cement and ceramic grains increase the non-evaporable water but decrease the calcium hydroxide. Estimations suggest that 20% replacement of cement by the micro ceramic powder indicates an economical benefit of 9.6% in concrete manufacture and a decrease of 6.62% specific energy consumption in Effect of chemical composition of clinker on grinding energy
احصل على السعر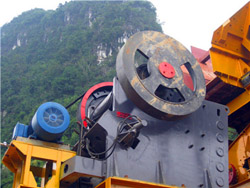
Analysis of individual and interaction effects of
These results are useful for the production of high-quality alumina powders in ceramic industries. Introduction The ball mill [[1], [2], [3]] is one of the most popular comminution machines used in ceramic powder processing to reduce the average and maximum particle sizes of starting powders, to alter their particle size distributions In addition, wheels with different abrasive grain sizes are also indispensable for the design of the multi-step process. It should be noted that diamond wheels are widely used in industry to machine hard and brittle materials such as ceramics, optical glasses and crystals [19, 25, 26].Moreover, the resin-bonded has good self Machining behaviors of glass-ceramics in multi-step high-speed grinding
احصل على السعر
Role of starch in the ceramic powder synthesis: a review
The main goal of this work was to demonstrate a broad range of starch applications in ceramic powder synthesis, and to point out that starch and its derivatives can successfully replace polyvinyl derivatives commonly used in ceramic formulations, as they are water-soluble saccharides, burn out more easily, reduce the exothermicity of the Afterward, they are shaped and cut to precise requirements and fired at extreme heat in temperature-controlled kilns. Firing removes the moisture and binders. With additional firing, powder Fine Ceramics Production Process Introduction to
احصل على السعر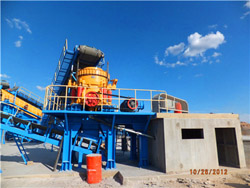
Ceramic Powder Preparation Solution
Ceramic powder preparation methods mainly include two kinds: Pulverization method: mechanical crushing (impact crushing, ball grinding, planetary grinding, vibration grinding, etc.), airflow crushing.Impurities, more than 1μm. Synthesis method: solid phase method, liquid phase method and gas phase method.Purity, The two micrographs are clearly similar, and show that the origin of defect in the sintered ceramic is the original defect in the powder compact. In this specific example, large pores create large pores in the sintered ceramics [3]. Table 2. Grouping of structures in powder compacts, their characteristics and significance on ceramic production.Processing defects in ceramic powders and powder compacts
احصل على السعر
Recycling of ceramic tiles waste and marble waste in
Both strong solid wastes, i.e., ceramic tiles waste and marble waste, should serve the purpose of recycling because of compact unit structures (Daniyal & Ahmad 2015; Ulubeyli and Artir 2015).Such practices not only guarantee the reduction in resources required for efficient waste management but also reduce the demand and production of Stabilized with yttrium oxide, after intensive grinding, for the production of ceramic pastes. The starting material was spray-dried zirconium powder partially stabilized with 3 mol% yttrium oxide (in the form of granules or particles), to which was added Methocel (viscosity increasing agent, its purpose is to maintain homogeneity and prevent3D Printing Ceramics—Materials for Direct Extrusion Process
احصل على السعر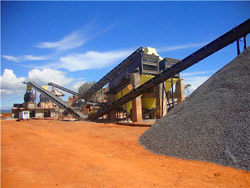
Process of fine milling for ceramic materials ScienceDirect
The production of very fine powders can be achieved by using modern grinding machines, e.g. stirred ball mills and vibration mills for wet grind- ing or jet mills for dry grinding processes. The *Paper presented at the Symposium on Ceramic Materials Research at the E-MRS Spring Meeting, Strasbourg, May 31 -June 2, 1988. more difficult Ceramic powder processing comprises of p owder pr oduction b y grinding/millin g, follo wed by production of green pr oduct, which is then fabricated to produce the final prod uct. A powder is a(PDF) CERAMIC MATERIALS: PROCESSING, JOINING AND APPLICATIONS
احصل على السعر
Material-Removal Mechanisms in Grinding Ceramics
Summary. This paper discusses material-removal mechanisms in grinding of ceramics using single-point diamonds and diamond wheels. The ground layers were analyzed using SEM, TEM and other inspection methods. Material pulverization was discovered on the surface layer of ground ceramics. A powder regime was observed ceramic sheets or tape, which can be cut and stacked to form multilayer ceramics for capacitors and dielectric insulator substrates. 11.7.2.5 Green Machining After forming, the ceramic shape often is machined to eliminate rough surfaces and seams or to modify the shape. The methods used to machine green ceramics include surface AP-42, CH 11.7: Ceramic Products Manufacturing US EPA
احصل على السعر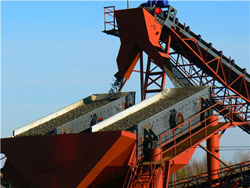
Effects of Grinding Methods and Water-to-Binder Ratio on
The reduction in the particle size of ceramic powder was less noticeable, as the specific surface area increased by cca 8% after the second stage of grinding. As a result, the activity index of biomass ash was enhanced from 102% to 112%, while the activity index of ceramic powder was kept constant at the age of 28 days.
احصل على السعر