
types of grinding mills in cement company
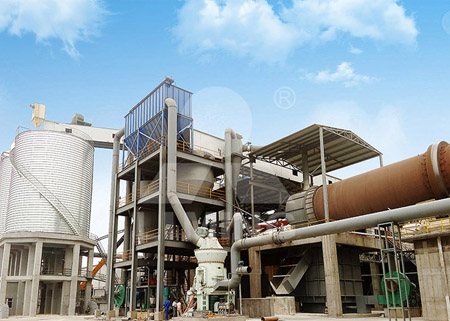
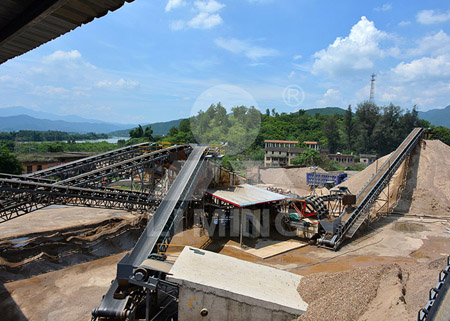
types of grinding mills in cement company
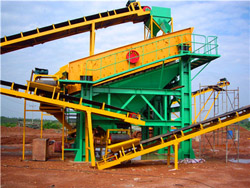
Energy-Efficient Technologies in Cement Grinding
This mill is a major improvement of the cement grinding systems known today which are ball mill, roller press (HPGR)/ball mill, In general, cement mill can both apply for dry cement production and wet cement production. Commonly, there are three hot types of cement mill in the cement industry: cement ball mill, Raymond mill, and vertical cement Cement Mill Cement Ball Mill Vertical Cement
احصل على السعر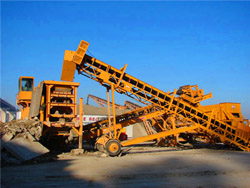
Common grinding mills in the cement industry ResearchGate
are several types of cement grinding mills that are used in cement manufacturing plants. Table 2, are the list of cement grinding mills and it grinding efficiency, [8][9][10].GRMK vertical cement mill has the advantages of compact structure and small volume. It mainly includes high efficiency separator, grinding rollers, grinding table, hydraulic The important role of vertical roller mills in the cement industry
احصل على السعر
Comparison of Separate and Co-grinding of the Blended
The main difference between separate and co-grinding of blended cement is the fact that co-grinding occurs interaction among the milled components. These Grinding is an essential operation in cement production given that it permits to obtain fine powder which reacts quickly with water, sets in few hours and hardens over a period of weeks....Overview of cement grinding: fundamentals,
احصل على السعر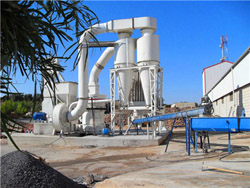
Grinding process optimization IEEE Xplore
The modular vertical roller mill for grinding cement raw material, cement clinker, and additives with an installed power of up to 12,000 kW was specifically The “work horse” of the cement grinding plant is the two-compartment ball mill, commonly called the tube mill. Significant advances in model development were Cement grinding optimisation ScienceDirect
احصل على السعر
Comparison of the overall circuit performance in the cement
In this study, in order to evaluate and compare the performances of different cement grinding technologies using the ball milling and high compression technology, Section snippets Experimental work. The same lots of Portland cement clinker and natural gypsum (CaSO 4.2H 2 O) were used in this industrial-plant-scale An industrial comparative study of cement clinker grinding
احصل على السعر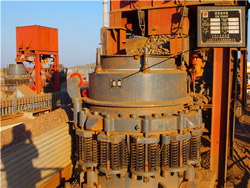
(PDF) Measurements of Vibration and Noise Level
Abstract and Figures. The aim of this article is to compare Vibration and Noise measurements caused by different types of Machines at cement factories with the standard evaluation criteria ofThe results implied that the production rate of the circuit and the 28-day strength of the cement could be increased by 24% and 3.5% respectively with the selection of an appropriate chemical. In addition, the use of chemicals may reduce the clinker consumption by 5% that is important regarding to CO2 emissions.The influences and selection of grinding chemicals in cement grinding
احصل على السعر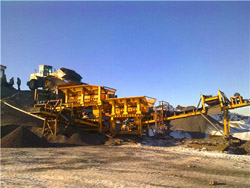
Cement Mill Cement Grinding Machine AGICO
Coal mill is the main equipment in the pulverized coal preparation process.Because calcining top-grade cement clinker requires a stable supply of coal powder as the fuel of cement kiln, and more than 85% of [Show full abstract] performances of these cement grinding technologies, industrial scale data were collected from HPGR-ball mill, VRM, Horomill and multi-chamber ball mill closed circuits.The(PDF) Pregrinding technology ResearchGate
احصل على السعر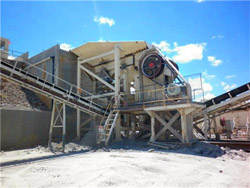
BALL MILLS Ball mill optimisation holzinger
type of installation: ball mills, combined in circuit with an air classification system of varying generations and sophistications. Depending on the local market situation and product portfolio, VRMs are the most common solution to grind raw materials and cement. Roller presses are used mainly in combination with a ball mill for cement grindingCompressive strength in early age was higher than in the case of ball mill type cement, however, the final strength were essentially the same. © 2016 The Authors. The comparison of the influence of separate or co-grinding this two components was performed on two types of mill. In both cases, the co-grinding seemed to be preferable Comparison of Separate and Co-grinding of the Blended
احصل على السعر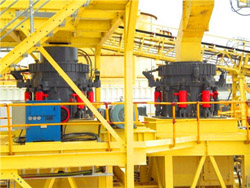
what are the types of grinding mill?-TY Industrial
It is mainly used in cement plant and relevant industrial departments for grinding other materials. Short tube mill is widely used for fine grinding of calcite, dolomite, quartz, zircon and other non-metallic minerals. 2. Raymond Mill. Raymond mill has the advantages of stable performance, simple process, convenient operation, large Spex branded grinding mills. Shatterbox® Ring and puck mill used for rapidly pulverizing brittle materials such as cement, slag, ores, and ceramics. Freezer/Mill® uniquely designed to cryogenically grind samples normally considered difficult or impossible to pulverize at ambient temperatures. Mixer/Mill® a high-energy ball millWhat are Types of Grinding Mills? [Video] Cole-Parmer
احصل على السعر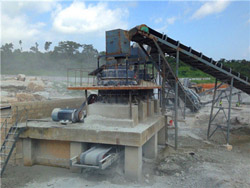
What kind of crushing equipment is needed to produce cement
Some common types of crushing equipment used in cement production include: Jaw Crushers: These are typically used for primary crushing of large chunks of raw materials such as limestone, clay, andIn addition, the vertical mill has the option of operating in initial grinding (raw materials) or final grinding (cement), which involves detailing some specific procedures.Chapter Six: Some Operating Guidelines Vertical Roller Mill
احصل على السعر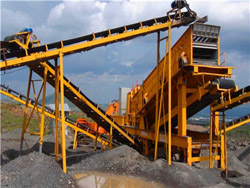
Overview of cement grinding: fundamentals,
Abstract. Grinding is an essential operation in cement production given that it permits to obtain fine powder which reacts quickly with water, sets in few hours and hardens over a period of weeksDue to limitation of the mill’s rotational speed, the smallest ball size is usually restricted to about 15 mm. Cement grinding using stirred mills (Pilevneli and Azizli, 1999) indicates that using smaller media (5–8 mm range) improves grinding energy efficiency up to 50% using stirred mills. For specialized types of cement, which are finerCement grinding optimisation ScienceDirect
احصل على السعر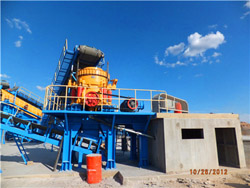
Process technology for efficient and sustainable cement production
Electrical energy only comprises between 10 and 15% of the overall energy demand for cement production but is a notable cost driver [4], [5].Over the last decades the average specific electrical energy consumption has decreased (Fig. 3) [6].However, there are counteracting effects: CO 2-emissions can be significantly The dry fine grinding experiments were carried out in a self-constructed batch-wise operated vertical stirred media mill shown in Fig. 1. The agitator is driven by a Dispermat AE-06 by VMA-Getzmann, Germany. The mill consists of a 1.6 L stainless steel grinding chamber (2). The chamber was designed with rounded edges to ensure a Impact of grinding aids and process parameters on dry stirred media
احصل على السعر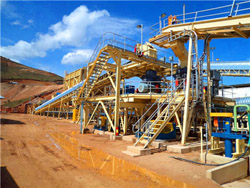
An industrial comparative study of cement clinker grinding
Section snippets Experimental work. The same lots of Portland cement clinker and natural gypsum (CaSO 4.2H 2 O) were used in this industrial-plant-scale experimental work to eliminate the potential effects of variations in the feed to the grinding systems. Chemical compositions of the clinker and the gypsum, measured by X-ray Cement ball mills are more suitable for cement grinding due to their particle size and shape, and have great advantages in cement hydration and later strength improvement, so cement ball mills are widely used in cement grinding. The company’s cement ball mill has 31 specifications and models with a cylinder diameter ranging from 2.2m to 4.2mBall Mill In Cement Plant Selling Various Types Of Cement Mill
احصل على السعر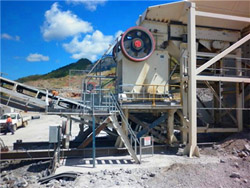
(PDF) Optimizing the control system of cement milling
The data include grinding of various cement types. The M Constrained Integral Gain Optimization (MIGO) loop shaping method is utilized to determine PID sets satisfying a certain robustnessThe study indicates that for a dry type cement production process, the carbon dioxide emission intensity for kiln feed preparation process is about 5.4 kg CO 2 per ton cement produced. In this study, the raw mill of a cement plant is considered and its performance based on the first and second laws of thermodynamics is investigated.Reducing energy consumption of a raw mill in cement industry
احصل على السعر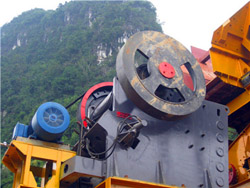
Cement Grinding Cement Plant Optimization
Cement grinding operation may be performed in one of the following mill setups. Ball and tube mills. Vertical Roller Mills (VRM). Roller press with Ball mill. Ball Mill. Ball mills with high efficiency separators have been used for cement grinding in cement plants all these years. Ball mill is a cylinder rotating at about 70-80% of critical
احصل على السعر